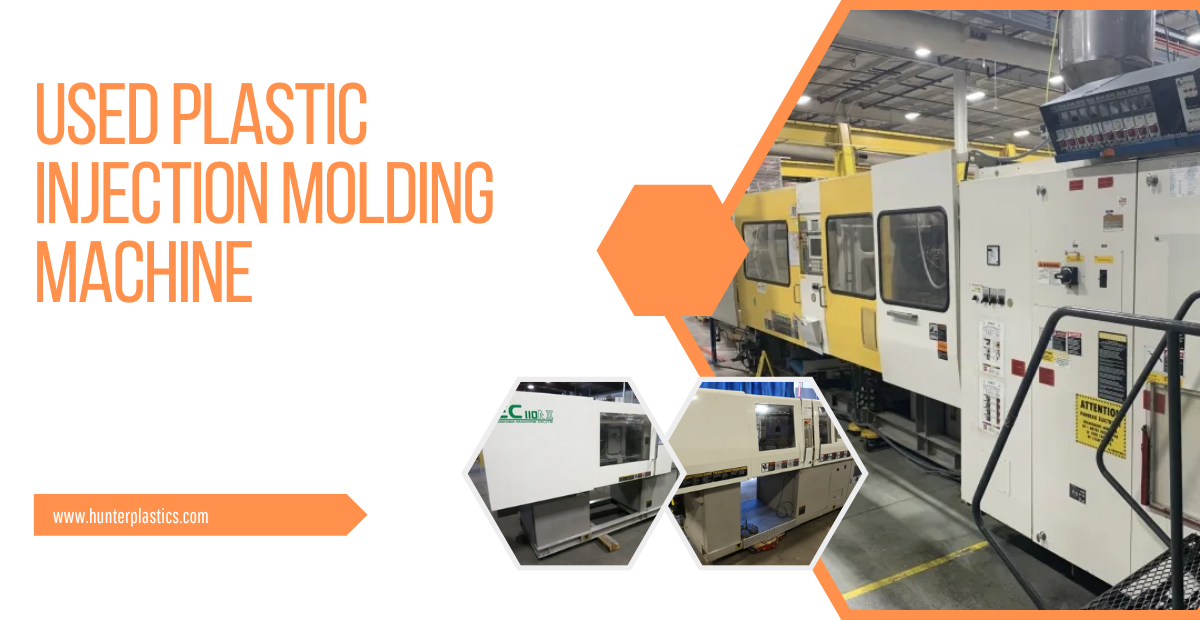
Purchasing used Husky injection molding equipment can be a cost-effective solution for manufacturers looking to expand their production capabilities without breaking the bank. However, like any pre-owned machinery, Used Husky Plastic Injection Molding Equipment can come with its own set of challenges. Understanding these common issues and knowing how to address them can help you maintain optimal performance and extend the life of your equipment.
1. Wear and Tear of Mechanical Components
One of the most common issues with used Husky injection molding equipment is the wear and tear of mechanical components. Over time, the repeated motion and stress on parts like screws, barrels, and platens can lead to degradation.
Solution:
Regular maintenance and inspection are crucial. Schedule routine checks to identify worn parts before they fail. Replace or refurbish components as needed. Using high-quality lubricants can also help reduce wear and prolong the life of moving parts. Additionally, consider investing in a maintenance contract with a reputable service provider who specializes in Husky equipment.
2. Hydraulic System Leaks
Hydraulic systems in injection molding machines are prone to leaks, especially in used equipment. Leaks can lead to inefficiencies, reduced pressure, and ultimately, machine downtime.
Solution:
Regularly inspect hydraulic hoses, seals, and connections for signs of wear or damage. Replace any components that show signs of leakage immediately. Keeping the hydraulic fluid clean and at the proper levels is also critical. Implement a preventive maintenance program that includes checking and tightening all hydraulic connections.
3. Electrical and Control System Issues
Used Husky injection molding equipment often comes with outdated or worn-out electrical and control systems. These systems are vital for the precise operation of the machinery, and issues here can lead to malfunctions or inconsistent product quality.
Solution:
Upgrade the control systems if possible. Modernizing the control panel can improve reliability and efficiency. Conduct regular checks on wiring, connections, and control units. Ensure that all electrical components are clean, properly insulated, and free from corrosion. Using surge protectors and voltage regulators can protect sensitive electronics from power fluctuations.
4. Temperature Control Problems
Precise temperature control is essential for the injection molding process. Used machines may suffer from faulty heaters, sensors, or temperature controllers, leading to inconsistencies in the molding process.
Solution:
Regularly calibrate temperature sensors and controllers to ensure accuracy. Inspect and clean heaters and thermocouples to maintain their efficiency. If you notice any irregularities in temperature control, investigate immediately to prevent defects in the molded products. Replacing old or malfunctioning temperature control units can significantly enhance the machine’s performance.
5. Insufficient Clamping Force
Over time, the clamping mechanism on used Husky injection molding equipment can lose its strength, leading to insufficient clamping force. This can cause issues with part quality and increase the risk of flash.
Solution:
Check the clamping system for wear and tear, and ensure that all mechanical parts are in good condition. Regularly measure the clamping force and adjust as necessary. Lubricate the clamping mechanism to reduce friction and wear. If the system is severely degraded, consider refurbishing or replacing the clamping unit.
6. Software and Firmware Obsolescence
The software and firmware in older Husky machines may be outdated, lacking the latest features and optimizations that newer versions offer.
Solution:
Consult with Husky or authorized service providers about updating the machine’s software and firmware. Up-to-date software can improve efficiency, provide better diagnostic tools, and enhance overall machine performance. Training your operators on the latest software functionalities can also maximize the benefits of these updates.
7. Cooling System Failures
The cooling system is crucial for maintaining the proper temperature of the mold and the hydraulic system. Used equipment may suffer from clogged or inefficient cooling channels.
Solution:
Regularly clean and descale cooling channels and components. Check the coolant levels and quality, and replace the coolant as recommended by the manufacturer. Inspect pumps, valves, and cooling lines for any signs of blockage or damage. Implement a preventive maintenance schedule to ensure the cooling system operates efficiently.
Conclusion
Investing in used Husky injection molding equipment can be a smart decision, offering substantial savings while maintaining high production standards. However, being aware of potential issues and taking proactive steps to address them is crucial for ensuring long-term reliability and performance. Regular maintenance, timely upgrades, and a thorough understanding of your equipment will help you get the most out of your used Husky injection molding machinery, keeping your production line running smoothly and efficiently.
By addressing these common issues with your Used Husky Injection Molding Equipment, you can maintain optimal operation and extend the lifespan of your investment, ensuring continued success in your manufacturing processes.