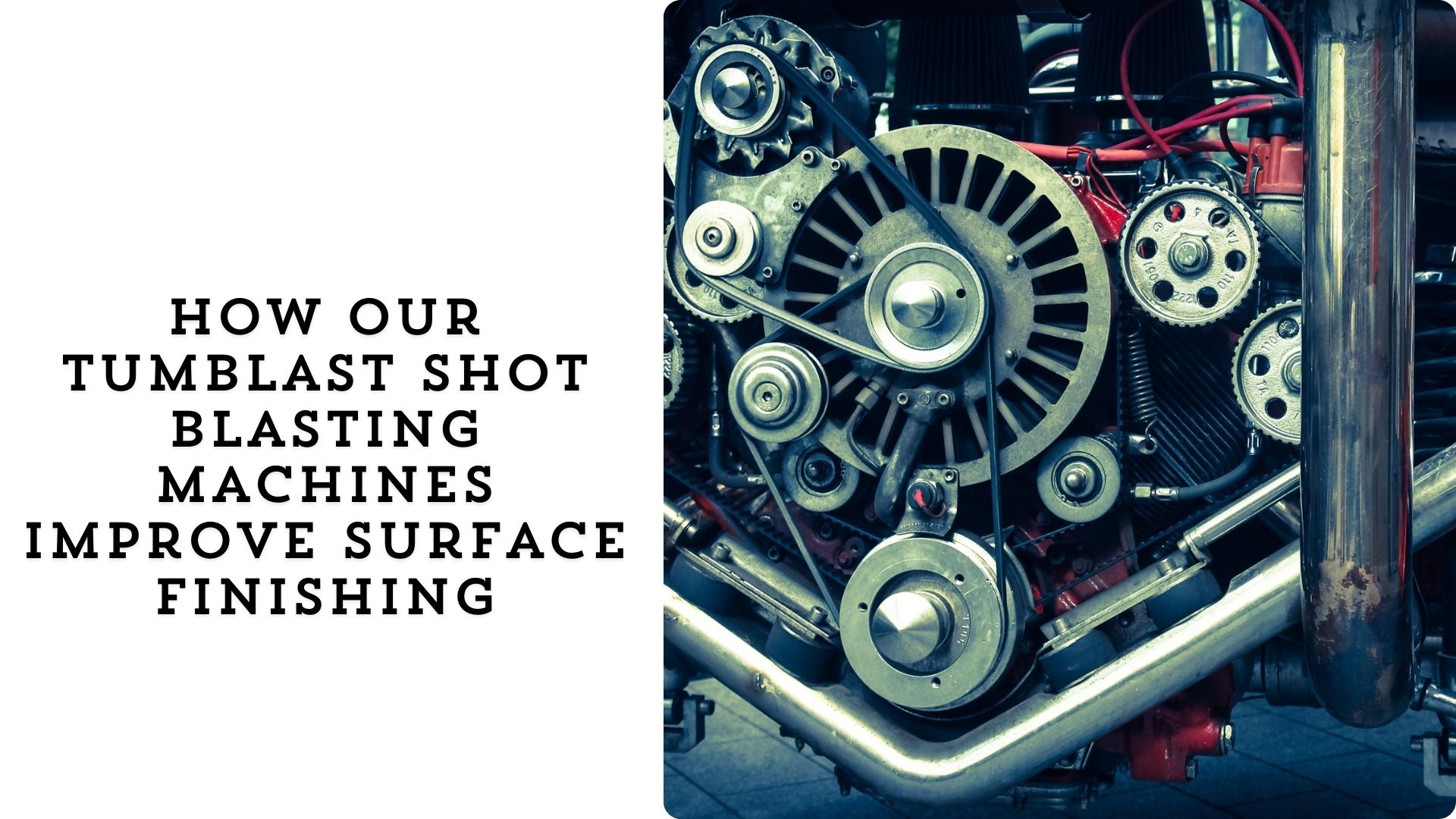
Surface finishing is a critical aspect of manufacturing and metalworking, determining the final appearance, durability, and performance of components. Among the various methods available for surface treatment, shot blasting stands out for its efficiency and effectiveness. Tumblast shot blasting machines, in particular, have revolutionized the way industries achieve superior surface finishes. This article delves into the intricacies of tumblast shot blasting machines and how they enhance surface finishing processes.
Understanding Tumblast Shot Blasting Machines
Tumblast shot blasting machines are a type of equipment designed to clean, strengthen, and polish metal surfaces by propelling abrasive media at high velocities. Unlike traditional shot blasting machines, tumblast machines feature a unique tumbling action that ensures thorough and uniform treatment of the workpieces. The term “tumblast” combines “tumble” and “blast,” reflecting the dual action that these machines perform.
Key Components and Working Principle
Blast Chamber:
The blast chamber is the heart of the tumblast machine. It houses the workpieces and the abrasive media. The chamber is designed to rotate, causing the parts to tumble and expose all surfaces to the blasting media.
Blast Wheel:
The blast wheel is a crucial component that accelerates the abrasive media and directs it towards the workpieces. The speed and intensity of the blast can be adjusted to achieve the desired level of surface treatment.
Abrasive Media:
The type of abrasive media used can vary depending on the application. Common media include steel shot, grit, and aluminum oxide. The choice of media impacts the finish, cleaning efficiency, and the material removal rate.
Dust Collection System:
Shot blasting generates a significant amount of dust and debris. The dust collection system ensures that the working environment remains clean and safe by capturing and filtering out airborne particles.
How Tumblast Shot Blasting Machines Work
The operation of a tumblast shot blasting machine involves several steps:
Loading:
Workpieces are loaded into the blast chamber. Depending on the machine’s design, this can be done manually or using automated systems such as conveyors or loaders.
Tumbling and Blasting:
Once the chamber is loaded, it begins to rotate, causing the workpieces to tumble. Simultaneously, the blast wheel propels abrasive media at high velocity onto the tumbling workpieces. This dual action ensures that all surfaces are uniformly treated.
Unloading:
After the blasting cycle is complete, the machine stops, and the cleaned workpieces are unloaded. The abrasive media is separated from the workpieces and recycled for future use.
Advantages of Tumblast Shot Blasting Machines
Uniform Surface Finish
The tumbling action of these machines ensures that all surfaces of the workpieces are exposed to the abrasive media. This results in a consistent and uniform finish, eliminating the risk of uneven treatment that can occur with static blasting methods.
High Efficiency
Tumblast shot blasting machines are highly efficient, capable of handling large volumes of workpieces in a relatively short period. The continuous tumbling motion allows for simultaneous blasting of multiple parts, enhancing productivity and reducing operational downtime.
Versatility
These machines are versatile and can accommodate a wide range of workpiece sizes and shapes. Whether dealing with small, delicate components or larger, more robust parts, tumblast machines can be adjusted to meet specific requirements.
Enhanced Surface Properties
Shot blasting not only cleans surfaces but also enhances their mechanical properties. The impact of the abrasive media induces compressive stresses on the surface, improving fatigue resistance and extending the lifespan of the components.
Cost-Effective
By improving the efficiency of the surface treatment process and reducing the need for manual intervention, tumblast shot blasting machines offer significant cost savings. The ability to recycle abrasive media further reduces operational costs.
Applications of Tumblast Shot Blasting Machines
Tumblast shot blasting machines are widely used across various industries, including:
Automotive Industry
In the automotive sector, these machines are used to clean and prepare parts such as engine blocks, crankshafts, and suspension components. The uniform surface finish ensures optimal performance and longevity of the parts.
Aerospace Industry
Aerospace components require precise surface treatments to meet stringent quality standards. Tumblast shot blasting machines provide the consistency and reliability needed to treat parts like turbine blades, landing gear, and structural components.
Foundries and Forging Shops
Foundries and forging shops use tumblast machines to remove scale, rust, and other contaminants from castings and forgings. This prepares the parts for subsequent machining, coating, or assembly processes.
Metal Fabrication
In metal fabrication, achieving a clean, smooth surface is essential for welding, painting, and coating applications. Tumblast shot blasting machines ensure that fabricated parts are free from impurities, enhancing the adhesion and durability of coatings.
Conclusion
Tumblast shot blasting machines represent a significant advancement in the field of surface finishing. Their unique design and operation offer numerous advantages, including uniform surface treatment, high efficiency, versatility, enhanced surface properties, and cost-effectiveness. By integrating these machines into their production processes, industries can achieve superior surface finishes that meet the highest standards of quality and performance. As manufacturing technologies continue to evolve, tumblast shot blasting machines will undoubtedly play a crucial role in shaping the future of surface finishing.