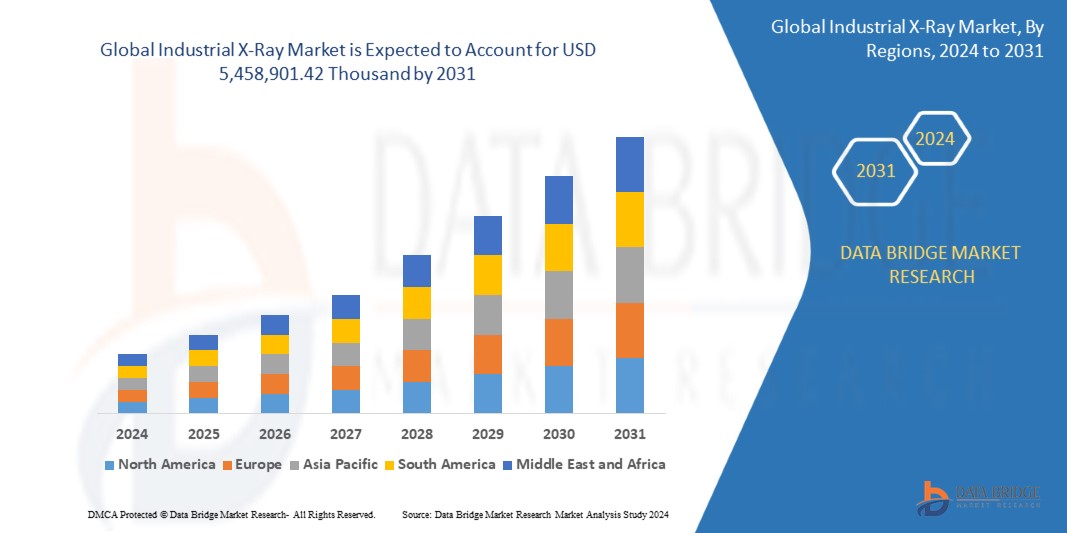
Industrial X-ray technology has revolutionized non-destructive testing (NDT) and inspection processes across a wide range of industries, from manufacturing and aerospace to automotive and electronics. By harnessing the penetrating power of X-rays, industrial X-ray systems enable engineers and technicians to examine the internal structure, integrity, and quality of materials and components without causing damage. In this comprehensive guide, we will delve into the principles, applications, and benefits of industrial X-ray technology, explore advanced techniques and imaging methods, discuss industry-specific use cases, and provide practical insights for optimizing X-ray inspection processes.
Understanding Industrial X-Ray Technology:
Industrial X-ray technology utilizes high-energy electromagnetic radiation in the form of X-rays to penetrate materials and produce images of their internal structure. X-rays are generated by an X-ray tube and directed towards the object or specimen being inspected. As X-rays pass through the material, they are attenuated or absorbed to varying degrees based on the density, thickness, and composition of the material. The remaining X-rays are captured by a detector, which converts them into electrical signals and produces a digital image of the internal features of the object.
Get More Details: https://www.databridgemarketresearch.com/reports/global-industrial-x-ray-market
Key Components of Industrial X-Ray Systems:
Industrial X-ray systems consist of several key components that work together to generate, control, and capture X-ray images:
-
X-Ray Source: The X-ray source, typically an X-ray tube, generates high-energy X-rays through the process of electron acceleration and collision with a target material, such as tungsten or molybdenum. X-ray tubes are available in different configurations, including stationary tubes, rotating anode tubes, and microfocus tubes, each optimized for specific applications and imaging requirements.
-
X-Ray Detector: The X-ray detector captures the attenuated X-rays that pass through the object being inspected and converts them into electrical signals. Common types of X-ray detectors used in industrial applications include scintillation detectors, photodiode arrays, and amorphous silicon detectors, each offering unique capabilities in terms of sensitivity, resolution, and dynamic range.
-
Manipulation System: The manipulation system, consisting of a motorized stage or gantry, allows for precise positioning and movement of the object or specimen relative to the X-ray source and detector. This enables multi-angle inspection, tomographic imaging, and 3D reconstruction of complex objects, enhancing the versatility and effectiveness of X-ray inspection techniques.
-
Control Console: The control console serves as the interface for operating and controlling the industrial X-ray system, including setting exposure parameters, adjusting imaging settings, and capturing X-ray images. Modern control consoles feature intuitive user interfaces, touchscreen displays, and advanced software functionalities for image processing, analysis, and reporting.
Applications and Benefits of Industrial X-Ray Technology:
Industrial X-ray technology offers a wide range of applications and benefits across various industries and sectors:
-
Non-Destructive Testing (NDT): Industrial X-ray inspection is widely used for non-destructive testing (NDT) of materials and components in manufacturing, aerospace, automotive, and other industries. X-ray inspection techniques, such as radiography and computed tomography (CT), enable detection of defects, discontinuities, and internal flaws in welds, castings, composites, and assemblies, ensuring product quality and integrity.
-
Quality Control and Assurance: X-ray inspection plays a crucial role in quality control and assurance processes, enabling manufacturers to verify the dimensional accuracy, structural integrity, and conformance to specifications of critical components and assemblies. X-ray inspection can detect defects such as porosity, cracks, inclusions, and foreign objects that may compromise the performance or safety of the end product.
-
Failure Analysis and Root Cause Investigation: Industrial X-ray technology is utilized for failure analysis and root cause investigation to identify the underlying causes of component failures, product defects, or manufacturing discrepancies. X-ray inspection enables engineers to examine the internal structure and condition of failed components, analyze fracture surfaces, and determine the mechanism of failure, aiding in the development of corrective actions and preventive measures.
-
Material Characterization and Research: X-ray imaging and analysis techniques, such as X-ray diffraction (XRD) and X-ray fluorescence (XRF), are employed for material characterization and research in academic, scientific, and industrial settings. XRD enables identification of crystalline phases, crystallographic structure, and phase composition of materials, while XRF provides elemental analysis and quantification of chemical composition in solids, liquids, and powders.
-
Reverse Engineering and Metrology: Industrial X-ray CT scanning is used for reverse engineering and metrology applications, enabling precise measurement, dimensional analysis, and 3D reconstruction of complex parts and components. X-ray CT scans provide high-resolution images and digital models of internal features, enabling engineers to extract geometric data, perform virtual cross-sections, and conduct detailed analysis of internal structures.
-
Product Design and Development: Industrial X-ray technology supports product design and development processes by providing insights into the internal architecture, assembly, and functionality of prototypes and early-stage designs. X-ray inspection helps engineers visualize design iterations, identify potential design flaws or manufacturing constraints, and optimize product designs for performance, reliability, and manufacturability.
Advanced Techniques and Imaging Methods in Industrial X-Ray:
Industrial X-ray technology encompasses advanced techniques and imaging methods that enhance the capabilities and effectiveness of X-ray inspection:
-
Computed Tomography (CT): Industrial X-ray CT scanning utilizes rotational X-ray imaging and computerized reconstruction algorithms to create 3D volumetric representations of objects and components. CT scanning enables non-destructive internal inspection, defect visualization, and dimensional metrology of complex parts, assemblies, and structures with high accuracy and resolution.
-
Digital Radiography (DR): Digital radiography is a digital imaging technique that replaces traditional film-based X-ray radiography with digital detectors and imaging sensors. DR systems offer real-time imaging, high sensitivity, and improved dynamic range, enabling rapid inspection of large areas, complex geometries, and diverse materials with enhanced image quality and diagnostic capabilities.
-
Phase Contrast X-Ray Imaging: Phase contrast X-ray imaging techniques exploit phase shifts in X-ray wavefronts caused by variations in material density and composition, enhancing contrast and visibility of subtle features and structures that may be difficult to detect with conventional absorption-based imaging. Phase contrast imaging is particularly valuable for imaging soft tissues, low-contrast materials, and fine details in biological and medical applications.
-
Dual-Energy X-Ray Imaging: Dual-energy X-ray imaging techniques utilize multiple X-ray energy spectra to distinguish between different materials, elements, or tissue types based on their differential absorption properties. Dual-energy imaging enhances tissue contrast, reduces image artifacts, and improves material discrimination in medical imaging, security screening, and material analysis applications.
-
X-Ray Fluorescence (XRF) Imaging: X-ray fluorescence (XRF) imaging techniques employ X-ray excitation to induce fluorescence emission from atoms in a sample, enabling elemental mapping, compositional analysis, and material characterization. XRF imaging provides spatially resolved elemental information and quantitative analysis of trace elements, contaminants, and alloys in diverse materials and samples.
Industry-Specific Use Cases and Case Studies:
Industrial X-ray technology is applied across various industries and sectors for a wide range of inspection and testing applications:
-
Aerospace and Defense: In the aerospace and defense industry, X-ray inspection is used for quality control of critical components, such as turbine blades, engine components, and structural assemblies. X-ray CT scanning enables detailed inspection of internal features, defects, and material properties in complex aerospace parts, ensuring compliance with stringent safety and performance standards.
-
Automotive Manufacturing: Automotive manufacturers utilize X-ray inspection for quality assurance of automotive components, such as engine blocks, cylinder heads, and brake systems. X-ray radiography detects defects, porosity, and inclusions in castings, welds, and assembled components, preventing quality issues, recalls, and warranty claims in automotive production.
-
Electronics and Semiconductor: In the electronics and semiconductor industry, X-ray inspection is essential for quality control and reliability testing of electronic components, circuit boards, and microelectronics assemblies. X-ray imaging detects solder defects, wire bonds, and interconnect failures in electronic devices, ensuring product reliability and performance in consumer electronics, medical devices, and automotive electronics.
-
Additive Manufacturing (3D Printing): Additive manufacturing processes, such as 3D printing, rely on X-ray inspection for quality control and process validation of printed parts and components. X-ray CT scanning verifies dimensional accuracy, internal porosity, and layer-to-layer bonding in additive manufactured parts, ensuring adherence to design specifications and performance requirements in aerospace, medical, and industrial applications.
-
Medical Device Manufacturing: In the medical device manufacturing industry, X-ray inspection is used for quality assurance of implantable devices, orthopedic implants, and medical instruments. X-ray radiography and CT scanning detect defects, voids, and foreign objects in medical devices, ensuring patient safety, regulatory compliance, and product reliability in the healthcare sector.
Best Practices and Considerations for Industrial X-Ray Inspection:
To maximize the effectiveness and efficiency of industrial X-ray inspection processes, consider the following best practices and considerations:
-
Define Inspection Objectives: Clearly define the inspection objectives, acceptance criteria, and quality standards for the X-ray inspection process based on the specific requirements of the application, industry regulations, and customer specifications.
-
Select Appropriate X-Ray Technique: Choose the most suitable X-ray technique and imaging method based on the material type, geometry, thickness, and defect characteristics of the object being inspected. Consider factors such as resolution, penetration depth, and contrast sensitivity when selecting X-ray parameters and equipment settings.
-
Optimize Exposure Parameters: Optimize X-ray exposure parameters, such as voltage, current, exposure time, and filtration, to achieve the desired image quality, contrast, and signal-to-noise ratio while minimizing radiation dose and image artifacts.
-
Calibrate and Validate Equipment: Regularly calibrate and validate industrial X-ray equipment to ensure accuracy, repeatability, and traceability of inspection results. Perform equipment checks, quality control tests, and calibration procedures according to manufacturer recommendations and industry standards.
-
Conduct Operator Training: Provide comprehensive training and certification programs for X-ray operators, inspectors, and technicians to ensure proficiency in equipment operation, radiation safety practices, and image interpretation skills. Invest in ongoing training and professional development to keep personnel updated on emerging technologies, best practices, and regulatory requirements in industrial X-ray inspection.
-
Implement Quality Assurance Measures: Establish robust quality assurance measures and documentation procedures to track inspection results, maintain traceability, and demonstrate compliance with regulatory requirements and customer specifications. Implement quality management systems, inspection protocols, and reporting templates to ensure consistency, reliability, and accountability in X-ray inspection processes.
Conclusion:
In conclusion, industrial X-ray technology represents a powerful tool for non-destructive testing, inspection, and analysis across a wide range of industries and applications. By harnessing the penetrating power of X-rays, industrial X-ray systems enable engineers and technicians to visualize and evaluate the internal structure, integrity, and quality of materials and components with unparalleled precision and accuracy. From aerospace and automotive manufacturing to electronics and medical device production, industrial X-ray inspection plays a crucial role in ensuring product quality, reliability, and safety in diverse industries and sectors. As technology continues to evolve and advance, industrial X-ray systems will continue to push the boundaries of innovation, enabling new capabilities, applications, and opportunities for quality assurance, process optimization, and product development in the digital age. Through continued investment in research, education, and collaboration, the future of industrial X-ray technology holds promise for further advancements, breakthroughs, and transformative impact on manufacturing, engineering, and beyond.