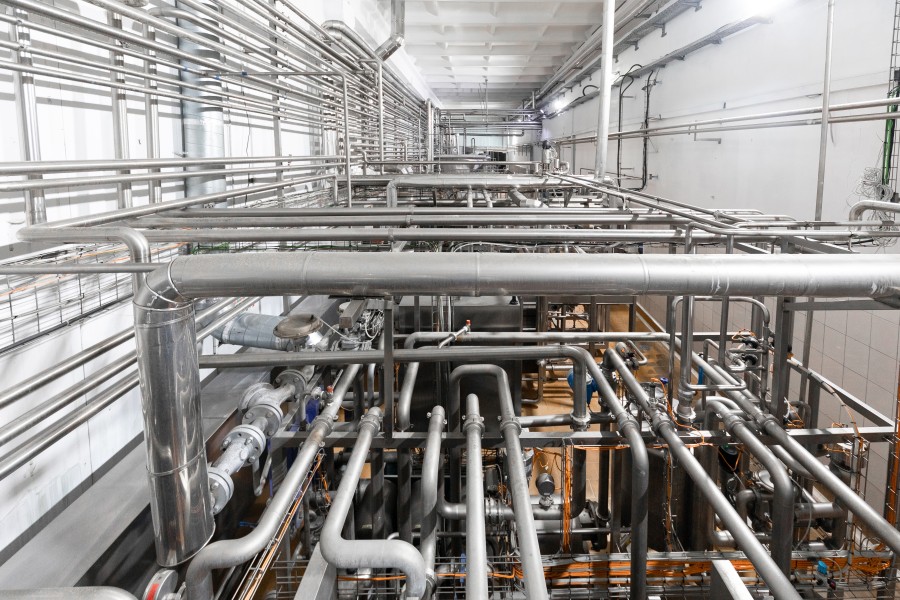
In the world of industrial infrastructure, efficiency reigns supreme. Every component, every system, is meticulously designed to maximize output while minimizing resource consumption. And in this pursuit of efficiency, the choice of materials plays a pivotal role. One such material that has garnered significant attention in recent years is Aluminium Pump Room Installation, particularly in the realm of pump room installations.
Aluminium pump room installations represent a paradigm shift in the way we approach industrial infrastructure. Gone are the days of bulky, cumbersome pump rooms constructed from traditional materials like steel or concrete. Instead, aluminium offers a lightweight, durable, and highly customizable alternative that is revolutionizing the industry.
In this comprehensive guide, we’ll delve into the world of Aluminium pump room installations, exploring everything from the benefits of aluminium to the step-by-step process of installation.
Understanding the Benefits of Aluminium
Before diving into the installation process, it’s essential to understand why aluminium has emerged as the material of choice for pump room installations.
Lightweight yet Durable:
Aluminium possesses a remarkable strength-to-weight ratio, making it ideal for applications where weight is a concern. Despite its lightweight nature, aluminium is incredibly durable, capable of withstanding harsh environmental conditions without succumbing to corrosion or degradation.
Corrosion Resistance:
Unlike steel, which is prone to rust and corrosion, aluminium naturally forms a protective oxide layer when exposed to oxygen. This oxide layer acts as a barrier, preventing further corrosion and ensuring the longevity of the pump room installation.
Customizability:
Aluminium is highly malleable and can be easily formed into complex shapes and configurations. This makes it incredibly versatile, allowing for the creation of bespoke pump room solutions tailored to the specific needs of the application.
Thermal Conductivity:
Aluminium’s excellent thermal conductivity ensures efficient heat dissipation, which is particularly beneficial in pump room installations where temperature regulation is crucial to maintaining equipment performance and longevity.
Step-by-Step Installation Guide
Now that we’ve established the numerous benefits of aluminium, let’s walk through the step-by-step process of installing an aluminium pump room.
Site Assessment and Planning
The first step in any pump room installation project is conducting a thorough site assessment. This involves evaluating the available space, assessing environmental factors such as temperature and humidity, and identifying any potential obstacles or challenges that may need to be addressed during installation.
Once the site assessment is complete, detailed planning can commence. This includes determining the optimal layout for the pump room, selecting the appropriate size and configuration of aluminium panels, and coordinating with suppliers to ensure timely delivery of materials.
Fabrication of Aluminium Panels
With the planning phase finalized, the next step is the fabrication of aluminium panels. This involves cutting, shaping, and welding aluminium sheets to create the various components of the pump room, including walls, doors, and access panels.
During the fabrication process, precise measurements are crucial to ensure that each panel fits together seamlessly during assembly. Advanced manufacturing techniques such as laser cutting and CNC machining may be employed to achieve the desired level of accuracy and precision.
Assembly and Installation
Once the aluminium panels have been fabricated, it’s time for assembly and installation. This typically involves erecting the framework of the pump room and attaching the individual panels using mechanical fasteners or welding techniques.
Care must be taken to ensure that each panel is properly aligned and secured to prevent air or water leaks. Additionally, provisions should be made for electrical wiring, ventilation ducts, and other essential components to ensure the functionality of the pump room once it’s operational.
Testing and Commissioning
With the pump room fully assembled, the final step is testing and commissioning. This involves conducting thorough inspections to verify that all systems are functioning correctly and that safety protocols are in place.
Pressure tests may be performed to ensure the integrity of the pump room’s structural components, while electrical systems are checked for proper wiring and grounding. Once testing is complete and any issues have been addressed, the pump room is ready for commissioning and integration into the larger industrial infrastructure.
Conclusion
Aluminium pump room installations represent a significant advancement in industrial infrastructure technology, offering unparalleled efficiency, durability, and customizability. By leveraging the inherent properties of aluminium, engineers and designers can create pump room solutions that are not only lightweight and corrosion-resistant but also tailored to the specific needs of the application.
As industries continue to evolve and demand greater efficiency and reliability from their infrastructure, aluminium pump room installations are poised to play a central role in meeting these challenges head-on. With their ability to withstand the rigors of industrial environments while maximizing performance and minimizing resource consumption, aluminium pump rooms are truly the future of industrial infrastructure.