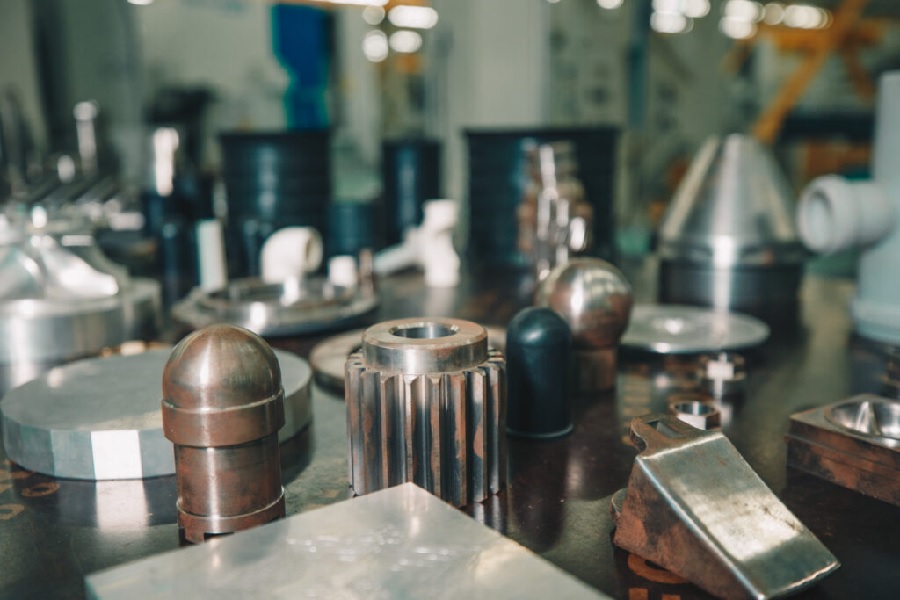
As the high-tech manufacturing industry continues to grow, the need for high-precision metal stamping parts has increased manifold. The metal stamping process changes a metal sheet into desired parts through one or more stamping operations.
Metal stamping parts suppliers rely on the design capabilities of the metal stamping manufacturing process including understanding different shearing edges.
Metal shearing is one of the integral operations of the metal stamping process and cuts out the material in the desired form. It is also called die cutting and cuts metal sheets without any traces of chips or damages like burning or melting of the metal.
The process uses the shear force similar to how scissors work to cut paper. However, shearing can cut metal rods as well. Some of the shearing operations in metal stamping are:
-
Blanking
-
Piercing
-
Trimming
Automotive, aerospace and consumer electronics are some of the prominent industries that require metal stamping parts suppliers. These parts frequently require shearing operations. In such processes, the metal part gets shearing edges until the fracture is visible between the upper and lower shearing edges.
Factors that affect the configuration of the shearing edge
The metal shearing edge depends on some crucial factors for the perfect configuration. Some of the imperative ones are:
Trimming Clearance
The trimming clearance is one of the key factors that determine the shearing edge quality and shape that metal stamping part suppliers and manufacturers rely on. It is represented as a percentage of sheet metal thickness. Mathematically, the horizontal distance between the upper and lower shearing edges is related to the radial distance between the round punch and die in hole punching.
Optimized trimming clearance means minimizing the uneven fractured edge condition. A high clearance is indicative of a better tool life as it means there would be less pressure on the cutting tool. However, with an increase in shear quality, a high clearance also increases the risk of deformation of the sheet material.
Material Used
The metal shearing edges depend on the quality of the material. High ductility, low strength, and homogeneity are all indicators of good shear edge quality, dimensional
Tool Wear
Tool wear means the shearing tools are gradually failing to perform optimally due to regular use. Therefore, high tool wear reduces the efficiency of the tool to trim the metal part with a good edge profile and dimensional accuracy.
The tool wear increased the burr height and burnish zone which affect the overall quality of stamping operations.
All the metal shearing operations result in a sheared metal edge that has four zones namely:
-
Rollover – Usually the bending operation causes a deformation during the metal stamping operation
-
Burnish Area – The sharp blades cause a vertical, rubbed edge that is usually called the burnish area
-
Fracture Area – The sheared metal may have a rough, angular surface. This is usually because of an abrupt transition from the smooth burnish area.
-
Burr – When there is excessive clearance, the cutting tools tend to become dull and create improper-sheared metals.
Different Forms of Shearing Edges
During the process of metal stamping, the shearing edge for the metal are of the following types:
-
Flat Edge Shearing:
Here the process includes sheet metal separation with two blades As the name and the process suggest this shearing can only cut the metal along a straight line. Here two blades work in parallel to create the desired straight line. The shearing edge is perfect for stamping parts with low width and high thickness.
-
Oblique Edge Shearing:
Oblique is different from a straight-line cut. It is rather an inclined straight line. Therefore, to create such a shearing edge the two blades are aligned in a manner that cuts the metal sheet as desired. Usually, the two blades obliquely intersect at a predefined angle, which the designer suggests.
The inclination affects the blade shears. Only a little portion is subjected to gradual shearing. Here the cutting force is lesser than that for the flat edge shearing.
Why do Metal Stamping Parts Suppliers Need to Know About Metal Shearing edges?
Metal shearing edges offer advantages like low scrap chips on the metal, no need for heating or melting, and minimal kerf production. The type of material decides whether metal shears are a feasible option or not. For example, metal shearing may not produce the desired results on hard materials.